Stainless steel welding: a successful weld
Stainless steel is a malleable, ductile metal, and in addition, it is aesthetically pleasing. It is frequently used for art and decoration as well as for DIY projects and boiler making. It is sometimes necessary to combine two or more stainless steel parts by welding for repairs or crafting.
Making a successful weld on stainless steel requires technical skills and know-how. In this article, we examine the various options for welding stainless steel.
What is stainless steel?
Stainless steel was first produced in 1913. This widely-used material is made from a low carbon steel base to which chromium, nickel and molybdenum have been added. By varying the percentages of alloying elements, four main categories are obtained.
- Austenitic stainless steel
- Ferritic stainless steel
- Martensitic stainless steel
- Austeno-Ferritic stainless steel, also known as Duplex.
The most frequently encountered are austenitic stainless steels, such as 304 stainless steel and 316 stainless steel (304L stainless steel and 316L stainless steel, classified according to the American AISI standard). The European standard reference is EN 10088-1.
The different ways of welding stainless steel sheets
Welding processes (including manual):
- MMA arc welding
- TIG welding
- MIG welding
- SAW torch welding
- Submerged arc
Machines capable of supporting automatic welding processes:
- Bench /Automatic plasma and TIG welding
- Robotic welding
Stainless steel can also be brazed with rods containing 40 % silver. This technique is more costly but gives a better result in terms of aesthetics and resistance of the assembled elements.
Manual welding of stainless steel
Before using any welding equipment, your safety is paramount, so plan your work and prepare carefully. Therefore, it is necessary to wear the following protective equipment:
- Work gloves
- Automatic welding mask
- Respiratory mask
- Welding apron
- Protective sleeves
- Safety shoes
We strongly advise all these accessories since your safety is imperative.
Furthermore, ensure that your various pieces are well secured and cannot move.
Once you are appropriately equipped and your work plan is ready, you are all set to weld!
MMA arc welding
If you have an arc welding machine, you can make a coated electrode weld, which is a fusion weld. Depending on the materials we intend to assemble, the electrodes differ. For example, in the case of welding stainless steel, we will need a stainless steel coated electrode to fuse two stainless steel pieces.
Arc welding of stainless steel is especially suitable for stainless steel sheets from one to ten millimetres thick.
As the name suggests, this process is based on an electric arc. The power supply produces an electric arc between an electrode and the base material (our stainless steel) by a short circuit. This arc creates incredible heat (up to several thousand degrees), which melts the metals and allows them to be fused.
To achieve this fusion, the stainless steel sheets must first be joined using a metal clamp which prevents them from moving during welding. Then, once the parts are in place, they must be electrically connected by a ground clamp.
In addition, the coated stainless steel electrode will be handled via the electrode holder. This electrode holder is completely insulated against heat, which allows you to control the electrode without danger, and, therefore, to bring the electric arc and weld to where you require.
Our tips:
Your safety is the priority, so wear protective clothing and equipment before using the welding machine. It is vital to protect your eyes because the slag of a stainless steel weld bead bursts as it cools and projects everywhere.
Arc welding requires manual dexterity, and the first attempts are often laborious. So practice is necessary when learning the correct technique to weld properly.
The welding station must be set up correctly, so read the instructions for your device carefully. You must also connect the station to the electrode and the parts to be welded (in general, + for the electrode and – for the ground clamp of the stainless steel panels to be welded).
For example, a specific inclination is required between the electrode and the surface to be welded. This inclination depends on the type of welding you want to perform (butt welding, inside angle welding, outside angle welding, etc.). It is also necessary to move along the weld at an angle.
In addition, when we bring the electrode close to the place we want to weld, we must withdraw slightly as the spark of the arc strikes, and then we must keep it the same distance from the metal. This step requires experience since the electrode melts gradually; therefore, you have to pay attention and adapt for a precise weld.
The electric arc is also used in other areas, such as plasma torches or spark plugs on ignition engines.
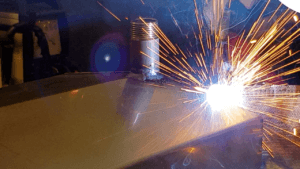
TIG welding in CAPIC’s workshops
TIG welding
TIG (Tungsten Inert Gas) welding is the most suitable manual welding for stainless steel. It is perfect for obtaining more delicate and stronger welds since the torch is compact enough to weld in places and angles that are difficult to reach by arc welding. However, it is also the most expensive type of welding.
TIG machines have several parameters, so make sure you use the correct ones for welding stainless steel. In addition, you will need gas. Therefore, you will require an argon cylinder suitable for TIG welding stainless steel.
One hand is used to wield the torch, while the other will be used to dip a filler rod. The latter must be compatible with the parts that we want to weld. Thus, if the pieces are in 304 or 304L stainless steel, the rod must be in 308L stainless steel, and if you are welding 316 or 316L stainless steel plates, it must be in 316L stainless steel.
TIG and MIG are also arc welds. They consist of the same elements: a weld pool, the protection and the filler metal. An electric arc carries out fusion, the protection is ensured by argon, and the filler metal is the stainless steel rod.
Your metal worktop must be connected by the ground clamp. Then, the electric arc is created at the end of the tungsten electrode, which will melt the stainless steel and cause a melting pool, in which you must approach the stainless steel rod manually. Thus, drops of stainless steel from your rod will form the weld between the two stainless steel plates.
TIG welding is, therefore, the most suitable since the torch is much more practical to handle. In addition, some torches control the gas supply with a button, while other welding stations have a pedal to heat the torch.
Our advice:
- If the liquid metal splashes, it means that the torch is not powerful enough, so increase the amperage.
- On the contrary, if the amperage is too high or you use the torch for too long on a specific point, you risk melting too much stainless steel.
- For welding, the optimal angle between a flat sheet and your torch is 75 degrees. We advise maintaining a distance of about 2cm between the end of your torch and the desired joint.
- After welding, it is essential to wait for the stainless steel and the torch to cool before handling and moving them. Then, you can sand the parts using an orbital sander and an abrasive disc for a clean finish.
MIG welding
MIG welding (Metal Inert Gas, also called GMAW) is mainly used to fuse very thick stainless steel parts and therefore for filling. It is less “clean” in the final result than TIG welding, but this solution is much less expensive.
MIG is also a form of arc welding. Again, we find the same elements: a weld pool, the protection and the filler metal. An electric arc carries out fusion, protection is ensured by argon gas, and the filler metal comes automatically from the torch (a wire melts during welding).
For MIG welding, it is, therefore, necessary to obtain supplies of stainless steel wire and argon gas.
The advantage of MIG is that you can do it one-handed since everything is included in the torch.
Our tips:
- To make a good weld, you must hold the torch at an angle of around 30 degrees.
- Do not move the torch too quickly or too slowly. If the movements are too fast, the stainless steel will not melt. On the other hand, if they are too slow, the stainless steel will melt too much.
- After welding, wait for the stainless steel and the torch to cool down before handling and moving them. In addition, remember to turn off the gas when you have finished welding.
- As MIG welding causes a fair amount of slag, brush it off with a special stainless steel wire brush.
Torch welding
We strongly advise against torch welding of stainless steel as this method is outdated.
The vast majority of results you can achieve with a torch are very disappointing, and the appearance will often look like charring or burning.
The settings of an oxy-acetylene torch for welding stainless steel are highly complicated, especially depending on the thickness of the sheets. In addition, stainless steel conducts less heat than other steels and has a high coefficient of expansion, which makes torch welding complicated.
If you still want to opt for this choice, here are our tips:
- The torch flame must be slightly carburizing.
- The joint and the filler rod must be coated with stripper (apply it with a brush).
SAW – Submerged arc – Welding under flux
As most of the technologies for welding stainless steel, SAW (Submerged Arc Welding) is a process based on an electric arc. The differences here are that the process is automatic, and the electric arc is covered by granulated flux. As the arc is submerged, there is no need for gas, as is the case with MIG or TIG.
This solution is versatile and mainly used for longitudinal and circumferential butt welds. We find these welds primarily in the construction of tubes and stainless steel pressure vessels. Since these are in high demand in the agri-food sector, many boilermakers perform this type of welding.
Automatic welding of stainless steel
Manual welding is adequate for small pieces or parts that are easy to handle.
However, it is sometimes necessary to weld much larger parts or more complex shapes, especially in boiler making.
In these instances, automatic welding is a better option as it leaves much less room for error.
Plasma table/stem welding, orbital welding and automatic TIG
A small automatic welding stem is ideal for making welds between stainless steel tubes or between tubes and plates since the process follows predefined paths. The process is similar to orbital welding since the latter consists of rotating an electric arc around a part without a break at least 360 degrees.
Automatic stainless steel bench welding
An automatic TIG welding bench is a practical solution when welding two sizeable stainless steel parts together, for example, in constructing a stainless steel tank. A cylindrical tank is composed of a top, a bottom and the body of the tank, which is a ferrule, or cylinder. The cylinder is often welded on an automated welding bench, once or twice, depending on the length of the base panels.
Robotic welding
A welding robot is undoubtedly one of the best-known processes in the world of industry, particularly in the automotive sector.
Robotic welding saves a lot of time and, therefore, productivity. These robots have automated functions and carry out repetitive tasks of positioning and welding parts.
Welding robots can carry out both MIG and TIG welding. In all cases, they perform extremely precise and quality welding.